Industry 4.0 with private industrial-grade wireless solutions.
Descripción de la publicación.
TELCO TECHNOLOGIES
3/10/20253 min read
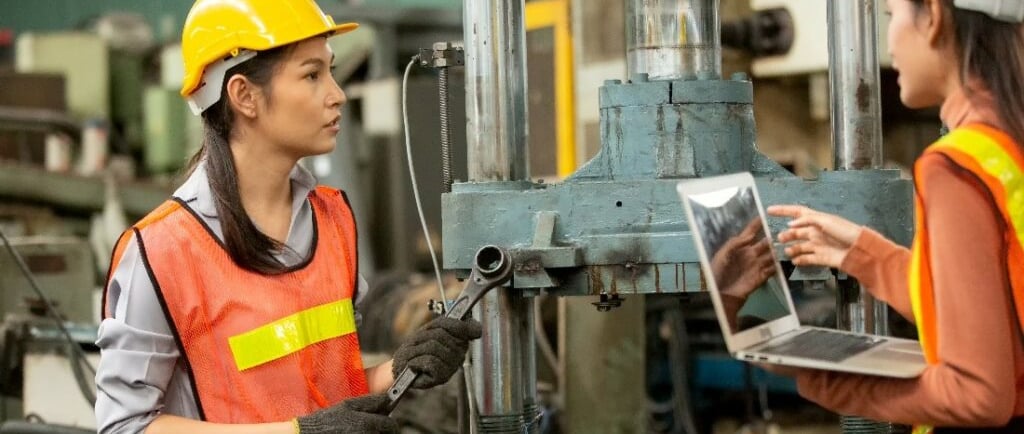
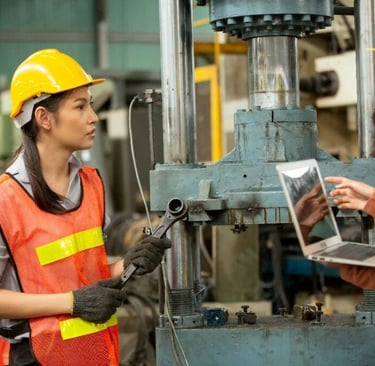
The manufacturing of chemical products is a complex process that involves more than just assembling parts. The quality of production and the need to collect and transmit data in real-time are some of the challenges faced by the chemical and plastic industries in general.
Among other things, chemical companies aim to increase productivity and worker safety in a more sustainable way. Digitalization and Industry 4.0 technologies can help them achieve these goals by allowing better control of their assets, generating meaningful insights from data, and enabling 24/7 operations.
Many manufacturers are taking their first steps toward a digital future through the implementation of the Internet of Things (IoT). According to predictions from ABI Research, by 2030, manufacturing and industrial companies will have deployed over 49 million IoT devices in their facilities. In the chemical industry, this number is expected to reach 4.8 million by 2030.
Spending by chemical companies on technologies such as predictive maintenance, digital twins, augmented reality (AR), and the Industrial Internet of Things (IIoT) will have a compound annual growth rate (CAGR) of 6% until 2031, and will focus on wireless technologies for large-scale areas (4.9G/5G).
The key to making the promise of Industry 4.0 a reality is to combine new applications and devices with reliable and ubiquitous wireless connectivity. This combination of capabilities can enhance the work of people, processes, sensors, robots, and legacy machines to achieve better results.
Accelerating digital transformation in the chemical industry.
The use cases for Industry 4.0 manufacturing can be divided into four main categories, within which there are specific use cases that can be implemented with private 4G/5G wireless networks.
Digital industrial campus
It involves use cases to digitize assets within and around the campus in order to monitor the environment and ensure safety.
Digital campuses include the use of sensor data to create digital twins of plants, facility management, security and surveillance with cameras, drones, and georeferenced perimeters, as well as uniform and global smart connectivity.
Automated plants
It involves connecting all the machines within the production processing area and monitoring them to improve communication and optimize performance.
In addition to machine interconnectivity, these plants implement IoT sensors, robotic cloud, and cobots between areas for M2M control (i.e., robots designed to interact physically with humans in work environments), as well as quality management to monitor and control the quality of products and processes using wireless HD/4K cameras. It also includes intelligent analytics to detect anomalies and errors.
Connected workers
4.0 applications help employees perform their work more efficiently.
Regarding connectivity, adding sensors, cameras, and mobile devices also contributes to efficiency. With the help of remote technical support, wireless HMI for machine control, and a set of PTT/PTV communication services, the exchange of information and real-time status updates is enabled.
Smart assets
The smart assets category includes AGV/AMR (Automated Guided Vehicles/Autonomous Mobile Robots), advanced AGVs with LIDAR and SLAM, for the supply of parts and materials to and from the warehouse and distribution center, as well as asset management for tracking purposes or machinery control.
The wireless connection of all the factory assets enables the collection of more data, which allows for greater supervision and analysis of operations to improve performance.
Private 5G for the largest chemical plant in Southern Europe
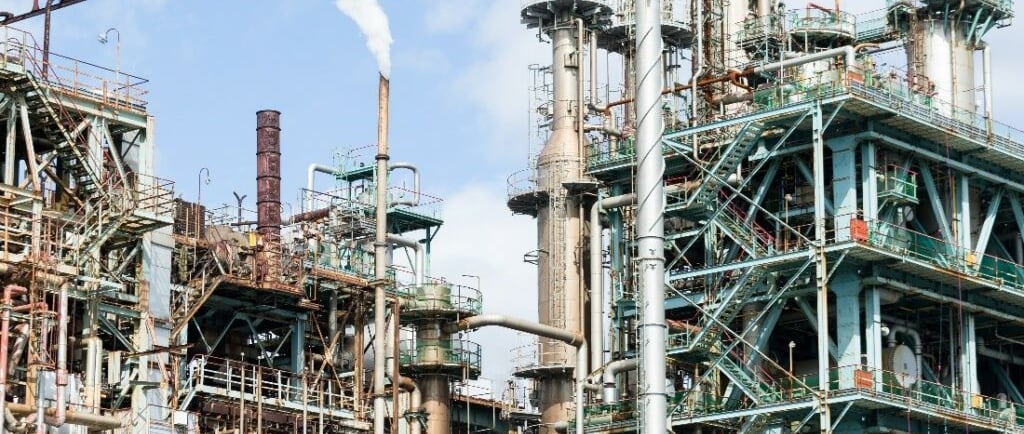
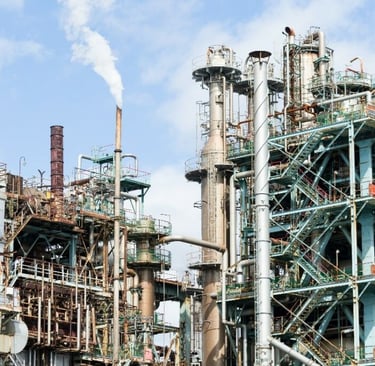
The chemical company BASF plans to install a private 5G network at its production center in Tarragona, Spain. Deployed in collaboration with Nokia and Cellnex Telecom, the new network will provide a platform to accelerate the digital transformation of operations. BASF chose this technology after an extensive trial that demonstrated the on-site 5G solution could meet the demanding connectivity requirements of several key applications:
Real-time license plate recognition for security, vehicle tracking, and vehicle guidance.
Worker tracking devices and panic buttons for emergencies and accidents.
AR/VR devices that provide real-time instructions to mobile workers.
Mission-critical group communications with real-time location tracking and push-to-talk and push-to-video services.
The company chose 5G technology because it increases data transmission speed by ten times compared to 4G and reduces latency to 1 millisecond, one-tenth of the current levels. Additionally, 5G provides the high availability and reliability required for critical applications and can connect and manage.
These capabilities will play a key role in BASF's digital transformation and address the company's industrial connectivity needs for the next decade and beyond.
In addition, the leap to the 5G era will allow the company to develop new applications in essential fields such as security and operations. It will also pave the way for automation enabled by IoT, big data analytics, augmented/virtual reality (AR/VR), and artificial intelligence.
Uruguay (HQ)
Paysandú 926
CP 11100
Montevideo
Tel: +598 2902 1477
© 2025 Isbel S.A., a brand Quantik®
Puerto Rico
República Dominicana
Av. Ana G. Méndez 1399, km 3
PR 00926
San Juan
Tel: +1 (787) 775-2100
Carmen C. Balaguer 10
El Millón, DN
Santo Domingo
Tel: +1 (809) 412-8672
Follow us